In 1908 the Commonwealth Government announced plans to build a small arms factory at Lithgow. The decision was favoured due to Lithgow’s proximity to essential resources (eg power, steel, transport, etc) as well as the security benefits afforded by the seclusion provided by the mountains. It is likely that Joseph Cook, formerly a Lithgow coal miner, and at that time, the Federal Minister of Defence, was influential in lobbying for the positioning of the factory in his home town.
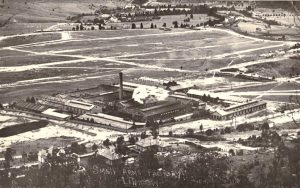
Six men were sent to the United States of America to the firm of Pratt and Whitney to learn how to make rifles. In December of 1909 Mr F.R. Ratcliffe of Pratt and Whitney arrived in Australia to assist in the planning of the factory.
On 10 January 1910, the site of the factory was inspected by Lord Kitchener and was officially opened on 8 June 1912 with Mr. A.C.Wright as the first manager of the factory.
Many of the materials required by the factory were supplied from other industries in Lithgow. Steel required for the production of guns, for example, was in part supplied by the Hoskins Brothers. Electrical power was initially generated on the site but was later obtained from the NSW Railways’ Power Plant.
Increasing demands were placed on the factory during the first World War with production doubling and then later re-doubling. The production of Lee-Enfield .303 rifles increased during this time from 15,000 per year to 80,000 per year. Over the period of the two world wars a total of 640,000 .303 rifles were made at the Small Arms Factory to assist the war effort (Brown 1989, p.86)
At the end of World War I, production began to decrease due to the decreased demand for armaments. As a result, the Armaments Factory began to diversify its production to include stream-lined wires and metal aircraft engine parts. By 1931 more than half of the factory’s production was linked to sound projection and sheep shearing machinery, Vickers Machine guns were also produced on site (Lithgow Public School 1947).
In the years before World War II items such as golf clubs, handcuffs, rifles and machine guns were made at the factory. When the war in Europe broke, production of armaments was again increased with the production of the Bren Machine Gun. This lead to considerable increases in employment at the factory.
A large forge and die sinking shop were constructed, reputedly the largest in the southern hemisphere, and new laboratories, boiler rooms and heat equipment were also introduced. The workforce at this time rose to 12,000 with the inclusion of increased shift work. This included 6,000 in Lithgow as well as an additional 6,000 in feeder factories established at Orange, Bathurst, Young, Forbes, Wellington, Cowra, Dubbo, Parkes, Portland and Mudgee to assist the Lithgow operations (Lithgow District Historical Society Notes).
The Small Arms Factory was one of the major employers in Lithgow for some time and as a result of the rising work force during World War II a suburb known as Littleton was established with ‘Duration Cottages’ to house both workers and their families. An additional railway station at Cooerwull was also established to facilitate commuter travel from the Blue Mountains’ towns.
After the war, tools, pencil sharpeners, sporting rifles and telephone parts have been produced. Operations at the Small Arms Factory have been significantly scaled down due to increasing government cutbacks.
Lithgow Tourism acknowledges and appreciates the History excerpts taken from the Draft Economic Development Strategy for Lithgow which was researched and compiled by Economic and Community Development Class, University of Sydney October 1996
For more information visit the Small Arms Museum Web site