In October 1875 iron smelting began in Lithgow under the direction of Enoch Hughes. The foundry was erected on Thomas Brown‘s Esk Bank property where ore was found just beneath the surface of the ground.
Hughes successfully encouraged James Rutherford of Bathurst, a principal shareholder and manager of Cobb and Co., Dan Williams a Canadian railway engineer who had worked on the Zig Zag and the Honourable John Sutherland the Minister for Public Works to join him in this steel making venture. By the end of 1876 the blast furnace was producing over 100 tons of pig-iron per week (Lithgow Public School 1947).
It was soon found that the success of the operation would be limited by cheap competition from overseas iron which was transported to the colony as ship’s ballast. The mill carried on for some time under a co-operative system but appeared to have failed. In a mark of frustration at the lack of protectionism measures for local industries, Rutherford blew up the blast furnace with two dray loads of blasting powder (Brown 1989, p66).
William Sandford who was associated with the early steel making operations in Mittagong, took over the operations from Rutherford in 1886 and made some initial successes in reviving the business by successfully puddling Australia’s first steel in 1900. Sandford was a strong lobbyist for Lithgow industry, encouraging the New South Wales Government to exclusively use locally produced iron and steel. In 1904 the government sought tenders from America, Europe and Australia to supply it with its iron and steel requirements. A condition of the contract was that all operations had to use local ores and that all works needed to be located within New South Wales. Sandford was awarded the contract in 1907.
In order to meet the obligations of his contract, Sandford built a new blast furnace with a capacity of 1,000 tons per week the funds for which were secured through a significant bank overdraft (Brown 1989, p.74). The bank was to shortly foreclose on Sandford’s loan, with the operations then passing to G & C Hoskins.
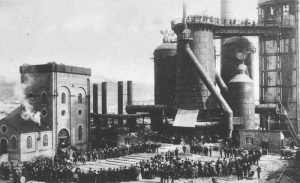
After George and Cecil Hoskins took over the Steel Works in 1908 the business began to thrive. In an attempt to make the local steel industry more viable, the Hoskins Brothers persuaded the government to pay a bounty for Australian produced steel. The Hoskins Brothers moved their operations from Rhodes in Sydney to Lithgow and began to make significant advancements.
Lithgow was to become renown for its steel production, with thousands of tons of steel being produced for the Trans-Australia Railway. In the first year of production, the Steel Works treated 51,000 tons of ore and employed 632 people (Lithgow Public School 1947). By 1926 the steel furnaces had turned out 178,000 tons of ore, resulting in 105,000 tons of pig iron (Lithgow Public School 1947).
Coke and limestone were both necessary requirements for the production of steel. Coke was required to generate the required heat levels to smelt steel, and the limestone was required to act as a flux to draw off the impurities from the ore. The success of the Lithgow iron and steel industry was dependent on the supply of these two resources.
Limestone for the Lithgow operations was obtained from Ben Bullen. Iron Ore was obtained from Coombing Park near Carcoar. This mine was originally opened as a copper mine by Thomas Icely in the 1870’s, as the copper was worked out it was discovered that a enormous body of Iron Ore surrounded the copper ore body. The mine was taken over by G & C Hoskins and a railway line built which opened on 27th April 1907.
Upon the closure of the Lithgow smelters the mine too closed in 1927 – it being uneconomical to transport the iron ore to Port Kembla. A enormous quantity of Iron ore was taken from this site over the years, often complete train loads, as well most through trains stopped & picked up loading from this site. This railway is still 100% intact. Possibly iron ore was trail mined at Irondale Colliery, Pipers Flat, but this has not been confirmed. Though a prospectus was issued stating that the Irondale Mine was to provide Iron Ore from a band of high grade Ironstone which was encountered in that mine.
Iron ore was also mined on Tunnel Hill at Marangaroo. And of course high grade silica flux was obtained from Newbolds Quarry & Brickworks at Marrangaroo, as well as the refractory bricks required for the Blast Furnaces.
Coke for the Blast Furnaces came from a variety of sources – Hoskins own Coke works at Lithgow, as well as Oakey Park Colliery, and possibly Zig Zag Colliery.
The supply of metallurgical coke, however was not sufficient, and additional supply had to be freighted from the south coast at great cost. This cost was exacerbated by the state government’s movement in 1919 to increase railway freight charges by 10% across the state (Brown 1989, p.83).
The lack of suitable coking coals, increases in railway freight charges and the inability of the Western District to supply sufficient quantities of good quality ore resulted in the demise of the Lithgow Iron and Steel industry. In 1932 the blast furnaces were removed from the site. The Hoskins Brothers at this time joined the Australian Iron and Steel Company and re-erected their steel works at Port Kembla.
The City of Greater Lithgow acknowledges and appreciates the History excerpts taken from the Draft Economic Development Strategy for Lithgow which was researched and compiled by Economic and Community Development Class, University of Sydney October 1996